Franzl and Bertl always find a way
Intelligent driverless transport systems
They look like two oversized USB sticks and curve around the Geberit production halls in Pottenbrunn (AT) without a driver. Franzl and Bertl are two intelligent transport systems. Other Geberit plants already have such plants in operation.
Franzl and Bertl are something like best friends. When Franzl has too much to do, Bertl rushes to his aid. If an obstacle stands in the way, Bertl warns Franzl. And vice versa. Like friends do.
Franzl and Bertl are driverless transport systems, the technical term for the two forklifts. On a tablet, their routes can be precisely defined and their task defined. After that, they need virtually no human intervention and transport pallets from logistics to production and back. Employees of the plant deposit pallets at the designated locations, the transport systems automatically transport them to the designated station.
No accidents
If they encounter a new obstacle on their route, they drive around it – and leave a note in the system to spare the other an abrupt stop. The sensors work excellently, accidents are excluded.
Franzl and Bertl have been working at the Geberit plant in Pottenbrunn, Austria, since 2020. Andreas Fink, Head of Logistics in Pottenbrunn, sees Agilox's transport systems as a big difference to other comparable ones on the market. “The developers come from the IT department of the automotive industry. Unlike usual, they started from the software and developed a device based on it. A bit like it was the case with Tesla,“ he says. This difference pays off – the devices are more intelligent than the competition, their software is “simple, flexible and independent“ to use.
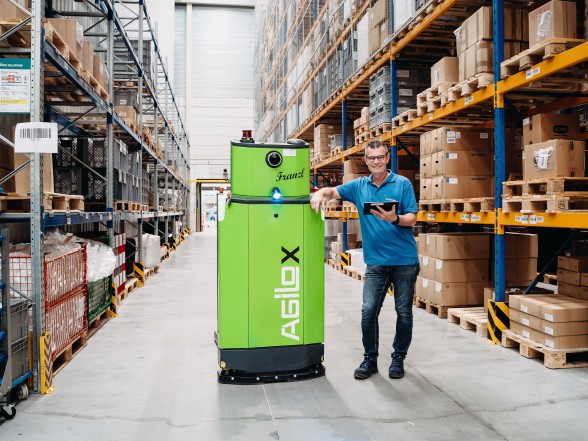
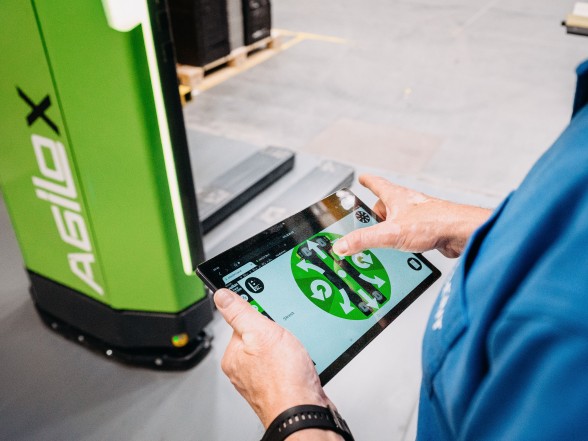
Thanks to Start-Up
He describes the development company Agilox as a start-up – it is less than ten years old. Since it is based in Austria, the communication channels are short. And the support is flawless, says Andreas Fink. And you hardly have to fall back on it. This is because most outages can be easily remedied by employees on site.
For example, by Thomas Bugl, Head of Shipping, Goods Receipt and Warehouse. To him, Franzl and Bertl look like two oversized USB sticks. “The two of them are recording an enormously high capacity utilization,“ he says. It is between 89 and 91 percent. External disturbances would be just 0.01 percent, technical malfunctions at 1.27 percent.
Short charging time
The charging time of the two is also minimal. If the battery life is coming to an end, the forklift goes to the charging station on its own initiative. Ten minutes there are enough to get him back in shape.
Andreas Fink also appreciates the fact that the two work via software that is independent of the company networks and only logged into the WLAN. “This makes the integration much easier – and you can ensure the entire control with a few tablets.“
For him, Franzl and Bertl, who are named after their respective project managers, are a groundbreaking step towards further automation. And this must take place not only in production, but also in logistics. Andreas Fink adds: “The two transport systems travel simple but time-consuming routes that would otherwise have to be covered by employees all the time. In this way, we can free them up for more demanding work.“