Potent fault detective
Quality management thanks to new software
Nothing escapes the camera. Its task: to find the smallest defects and flaws in the freshly produced actuator plates. Thanks to newly introduced software, the data collected can be evaluated better than ever.
The ready-assembled actuator plates roll down the conveyor belt. They slide into a “black box“ shortly before the packaging line at the Geberit plant in Jona - and come out exactly as they went in. However, the process is not without consequences.
The box contains cameras that analyse the condition of the dewy actuator plates under ideal lighting conditions. Software checks the images on the basis of a number of parameters - for example, whether the logo is neatly positioned, the surface is nice and even or the edge finish is right, depending on the model. “Thanks to a data matrix code on the back of the actuator plate, the system automatically recognises which model is currently being run through and which test steps it has to carry out,“ says Christian Landolt, project manager for quality assurance. And then it decides whether the piece is sorted out.
Much more potent
This has been the status quo for many years. The QualiVision systems have been installed at the Jona plant since 2008. But as of November 2021, they have become many times more potent. This is because doctoral student Arne Seeliger, who oversees digitisation projects at Geberit, has developed software together with a team that evaluates the mountain of data from the cameras.
This mountain of data is huge. The system uses the images to automatically identify which machine or tool is the cause of a problem – and where that problem is exactly.
Short- and long-term advantage
Making better use of all this data has two advantages, according to Arne Seeliger - one short-term and one long-term. The short-term: “We can programme the software to sound an alarm when a threshold value of rejects is exceeded for a product.“ Then the responsible persons receive a notification on their computers, or their mobile phones and they can quickly identify and remedy the source of the error. “We now have transparent process monitoring and are informed of irregularities in real time,“ says Christian Landolt.
Economical optimisation
According to Christian Landolt, this has already led to numerous process optimisations. This is also reflected economically. “If we assume a ten-percent reduction in subsequent errors, for example, this results in a cost-saving potential of a nice five-digit amount annually,“ says Arne Seeliger. “And that's for just one of three product lines, using a conservative estimate.“
The long-term benefits of the still young software will steadily increase within the next few months. According to Arne Seeliger, this involves the evaluation of the entire data pool over longer periods of time. “For example, we can find out which errors occur most frequently.“ Even if these data analyses are only gradually taking place, the innovation has already proven its worth.
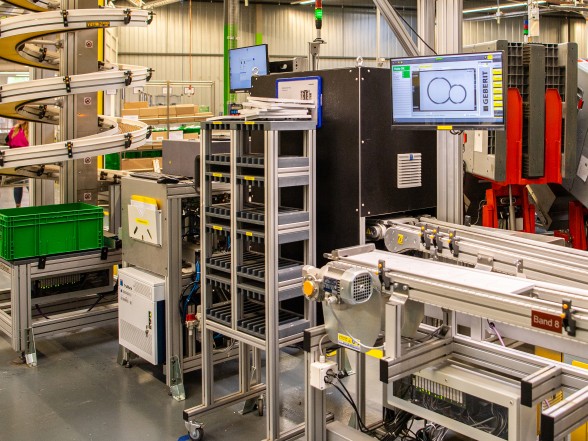
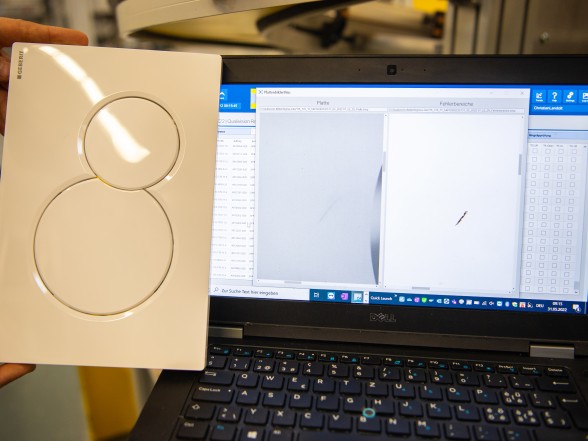