Responsible plastic processing
Geberit meets the challenges with aplomb
Preventing the loss of plastic granules during production and recycling plastics wherever possible are two topics that are close to Geberit’s heart.
Geberit manufactures high-quality products made from plastic. In doing so, it uses the product material in the most targeted and economical way possible. Plastic offers many benefits from a sustainability perspective as it is light, robust and durable, among other aspects.
Recycling plastics
Ever since the early 1970s, for example, scrap arising from production in Rapperswil-Jona has been collected and recycled. For around 20 years, the company has also been using recycled plastic regranulate for certain components. These include the mounting frames for actuator plates and various components installed in fill and flush valves. The quantities used are growing all the time, with around 1,000 tonnes of plastic regranulate now processed across the Geberit Group every year.
Geberit purchases the recycled material – primarily ABS (acrylonitrile-butadiene-styrene) that has been recovered from electronic scrap – on the market in the same way as new plastic granules and then shapes it into the desired form via injection moulding to make the new components. However, the anthracite grey colour of the plastic limits the possible uses and means it cannot be used on visible products.
Every granule counts
Another objective is ensuring that plastic granules used in production do not pollute the environment. To reinforce these efforts, Geberit joined the Operation Clean Sweep (OCS) initiative at the end of 2020. OCS is an international initiative promoted by the plastics industry dedicated to preventing the loss of plastic granules, flakes and powder and ensuring that they do not pollute the environment.
All Geberit plastic-processing plants are participating in this initiative and are required to define and implement improvements to avoid the loss of granulate.
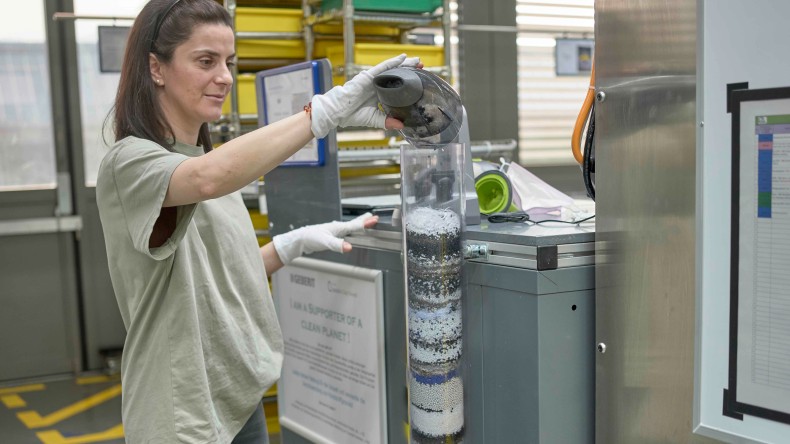