Shift starts at dawn
With machine setter at work
Machine setter and shift supervisor Tobias Höhn is up early: he starts in the production halls in Rapperswil-Jona (CH) before sunrise. Whether it's malfunctions, machine set-ups or quality controls – he and his team keep the operation of 60 injection moulding machines running. An early shift in pictures.
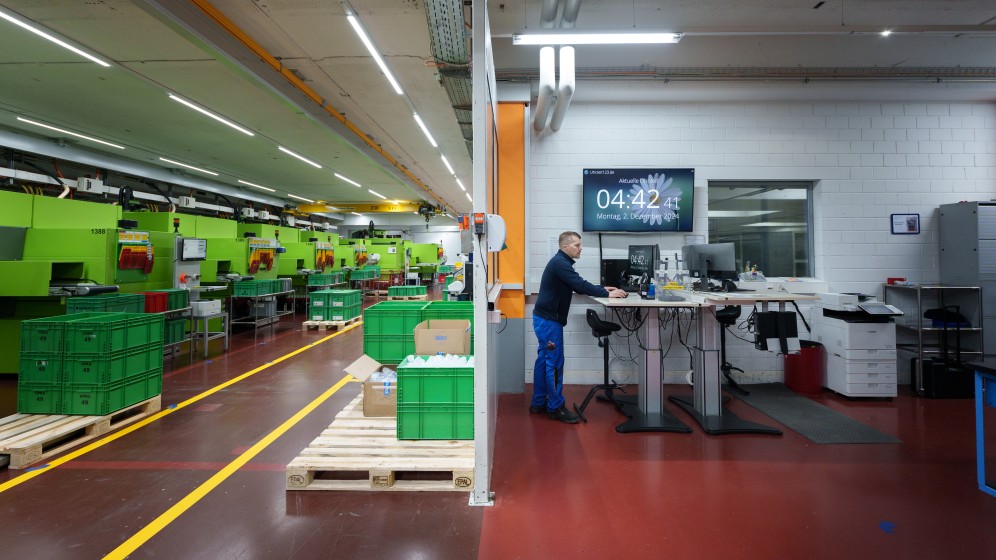
Shortly before 5 a.m., Tobias Höhn starts his early shift at the company's headquarters in Rapperswil-Jona. As a machine setter on the production line for drainage components, he is used to getting up early. He checks the computer for any malfunctions, which machines need to be retooled and how many employees are available.
He and his team are responsible for the smooth operation of 60 injection moulding machines.
On a tour of the production facility, the 36-year-old places so-called Kanban cards on the injection moulding machines, which contain precise information about the production order.
Around 7 a.m. there is a little refreshment at the snack vending machine in the break room. It is still dark outside.
At 8.15 a.m. the so-called Puls meeting takes place, where scheduling, shift management, logistics, production management and maintenance exchange information on productivity, production waste and machine malfunctions of the last 24 hours.
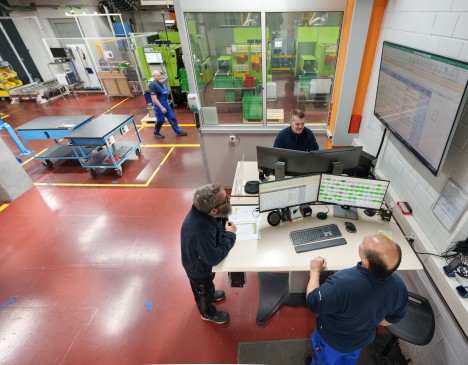
Shortly before 9 a.m. the phone rings. A colleague needs support because an injection moulding machine reports a problem that is not recognizable at first glance. Routine work for Tobias Höhn. “It never gets boring because new problems arise every day and every machine is different.“
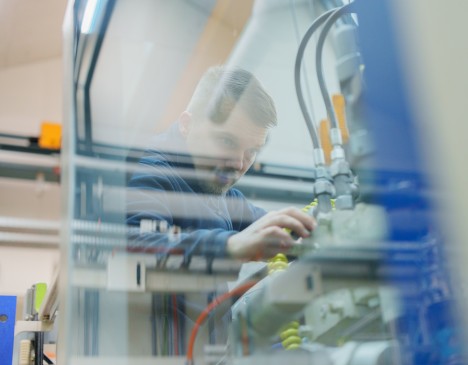
Around 10 a.m. an injection moulding machine must be converted according to plan. Tobias Höhn orders the tool, i.e. the new injection mould, from the dispatcher shortly before it is delivered to the production hall.
Using the indoor crane, he carefully lifts the tool, which weighs several tonnes, into the air. The manoeuvre is not without danger. If the speed is too high, the tool can swing out or hit the ground and be damaged.
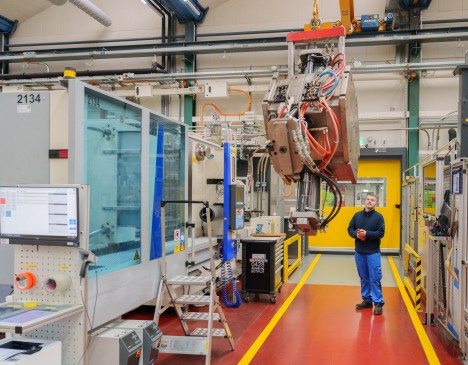
10:45 a.m.: The final steps are taken to clamp the tool in the machine. The one-hour time slot is very tight. The job is only completed when the machine has been running smoothly for an hour.
Quality control follows the changeover: After the first fitting has cooled down, Tobias Höhn carries out the first sample inspection on the test bench.
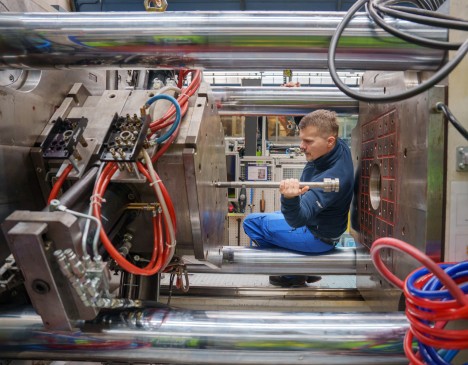
All angles, lengths, thicknesses and diameters must meet exact specifications before the fitting can be used on the construction site. “A wrong angle in this fitting can result in the water not draining properly.“
12 noon: Shortly before the end of his shift, the 36-year-old looks at the personnel planning. Since the beginning of 2025, he has held the position of shift supervisor. A challenge he enjoys. “The company invests in its employees, and I appreciate that.“
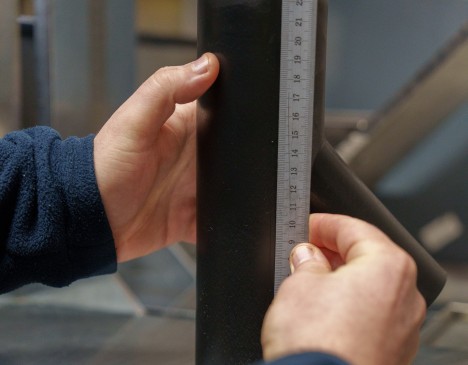