"Understanding the big picture"
Further training at the ceramics plant
At the Swedish ceramics plant, employees go back to school: Office and production employees gain an in-depth insight into the production of sanitary ceramics at the in-house academy.
Many process steps and a lot of knowledge are required to produce sanitary ceramics. However, very few employees are familiar with the entire process. Many only come into contact with individual steps in their day-to-day work.
The Geberit ceramics plant in Bromölla, Sweden, has set up the Pressure Casting Academy for this purpose. Here, production and office employees attend the Geberit training programme together. They go through ceramic production from A to Z and look beyond their own horizons. This promotes mutual understanding and ultimately leads to quality improvements. Contrary to what the name might suggest, the training is about much more than the modern pressure casting technology used at Geberit in Sweden, Finland and Poland.
An interview with the Academy's trainer, Joachim Lindberg, and two employees: Amanda Säll, Project Manager Products and Robin Efverman, employee at the casting line in production.
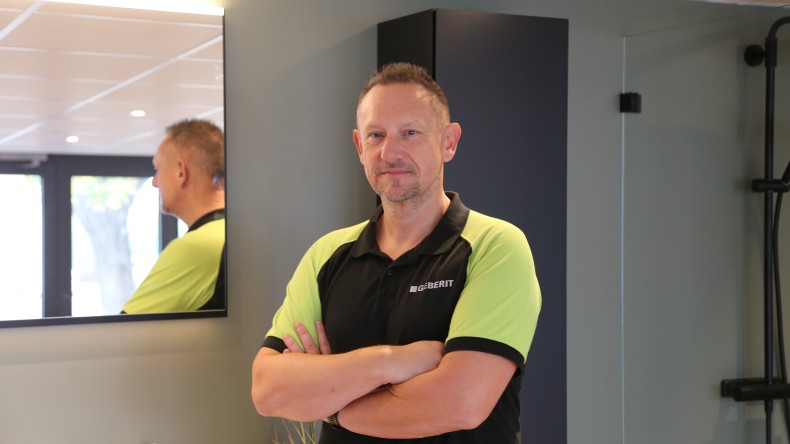
Joachim, what is the aim of the academy?
Course participants should understand how the ceramic process works from A to Z. This goes beyond their own area of responsibility. It improves mutual understanding of the individual process steps such as raw material purchasing, casting or mould production. By exchanging ideas, we understand what we can do together to further improve quality. Of course, it's also about passing on our extensive knowledge of ceramics internally.
How should we imagine such a training course?
It is a mixture of theory in the meeting room and practice in the production plant. We go through the process step by step, from the raw material to slip production, drying, glazing, firing and the finished product. We also look at each process directly in the production environment and discuss the respective challenges.
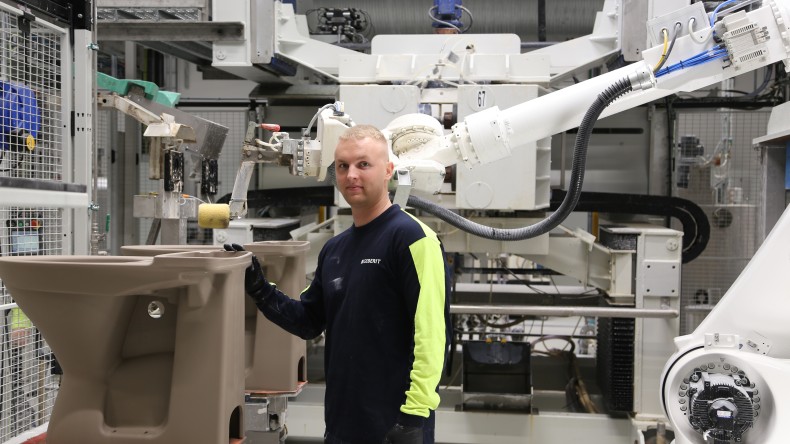
Robin, you took part in the academy, what are you taking with you?
I now understand the big picture and know how my work on the casting line contributes to the entire manufacturing process. I've worked in different areas of the plant and know a few process steps, but when people around me asked me how to make a toilet, I wasn't able to explain it well before the academy. It's like a jigsaw puzzle: now I understand how the individual pieces contribute to the overall picture.
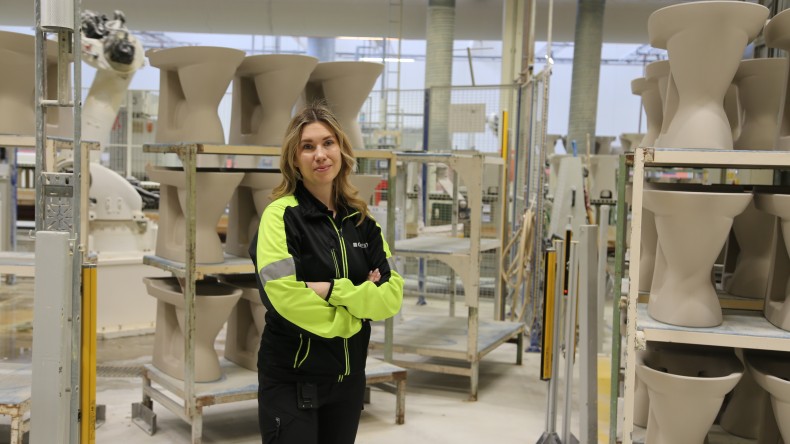
Amanda, you will be attending the training soon. What are your expectations?
I have already heard from my colleagues that they have learnt a lot. As I have worked in production plants before Geberit, but do not come from the ceramics industry, I hope to gain a deeper insight into the manufacturing process. In particular, I'm not yet very familiar with the production of moulds for the pressure casting process.
What do you think of this training programme?
Robin Efverman: We immersed ourselves in every step of the process. I appreciate that they took the time to do this. I can therefore definitely recommend the Pressure Casting Academy to my colleagues.
Amanda Säll: I'm very excited because I always find it interesting to learn new things. Knowledge is important to inspire people and motivate them to find new solutions.